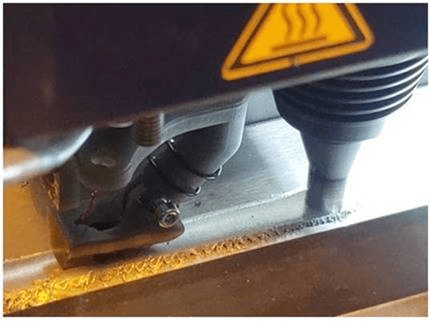
The STWIN project, coordinated by CIDAUT, will develop a flexible friction stir welding (FSW) system capable of automatically fabricating complex structures, for a variety of joint configurations, and for a range of steel grades and thicknesses used in the metal construction, automotive and transport sectors.
The project will address the need to improve productivity in the metalworking sector, improvement of the working conditions for welders and operators and the shortage of skilled welding personnel in Europe. This will be achieved by exploiting the specific advantages of the friction stir welding process, in combination with real-time quality control, based on innovative non-destructive testing and their integration with artificial intelligent and smart digital twin solutions. This will lead to a zero-defect manufacturing approach ensuring robustness, stability and repeatability of the process.
In FSW, a rotating tool is pressed into the gap between two parts. The friction between tool and parts produces heat, which leads to plasticising of the materials. The tool is then moved along the joint line. The combination of translation and rotation of the tool transports the material behind the tool, thus creating the joint.
In STWIN, a novel real time monitoring and control system will be built and demonstrated. The intention is to use the measured process parameters like rotation speed, forces, complemented with the measurements by a smart combination of sensors. These relationships will be used by closed-loop AI control algorithms, which will enable real time adjustment of process parameters, guaranteeing an improved joint quality, towards a more sustainable and defect-free production.
The research leading to these results has received funding from Horizon Europe under Grant Agreement nº 101112504.