by cidaut | Feb 17, 2021 | MOBILITY, Sin categoría
Cidaut is involved in Avangard project whose main objective is to develop advanced manufacturing solutions tightly aligned with business needs and oriented to the assembly of electric urban vehicles: 4 passengers’ cars, vans and bicycles. To achieve this ambitious target some innovative solutions are been applied both in the physical and digital ambit. From the physical point of view robotized integration of laser cutting-shaping –welding for 3D components, supersonic deposition of metallic powders for high speed 3D printing and large volume and high-speed 3D polymeric printing are the most relevant solutions.
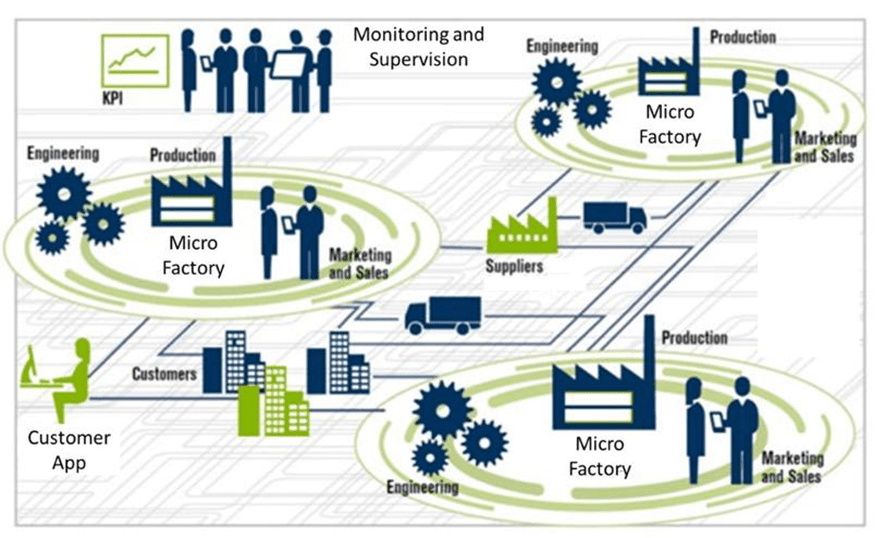
But today’s article aims to focus the attention on the digital solutions. Avangard pretends to digitalize the whole manufacturing and delivery process. From an electronic device, the client will be able to configure the vehicle, make the purchase order and follow the evolution of the vehicle manufacturing, assembly and delivery. At the same time, the manufacturing system is able to receive the order and decide the most suitable microfactory of the system to manufacture this vehicle attending to location, work load, availability of goods and environmental impact.
To warranty the security, privacy and authenticity of the whole process it is needed, among others, the application of blockchain solutions, that are being developed ad-hoc for Avangard project. The infrastructure of the complete system is based on IoT (Internet of Things) solutions. Despite the large advances in the last decades, centralized cloud services are vulnerable to security attacks.
The solution precludes the use of trustzone-based architecture to support cryptographic operations and tamper-proof memory for the secure storage of sensitive data. Thus RFID/NFC can provide a unique identity to the connected devices to warranty trustiness and tracking through the blockchain. Immutability technologies are used to generate real-time access control, restricting connection only to authorized devices to warranty the privacy of the system.
Acknowledgment
The research leading to these results received funding from the European Union (EU) project AVANGARD (GA #869986).
by cidaut | Dec 14, 2020 | MOBILITY
The aim of Avangard is to design a microfactory for the production of electric cars and bikes applying Industry 4.0 solutions and minimizing the footprint of both the production and use phase of the vehicles. After the first third of this three years project, the first prototypes of electric cars have been produced and the bicycles will come soon. Taking advantage of the modularity of the vehicle design, the prototypes correspond to different configurations: two standard four seat vehicles and two vans have been manufactured, in the case of the four seats vehicles one of them corresponds to the short length one, while the other is track extended. In the case of the vans the difference among them is the installation of photovoltaic panels in the external surface of one of them, which allows 20 additional kilometres range thanks to the solar irradiation.
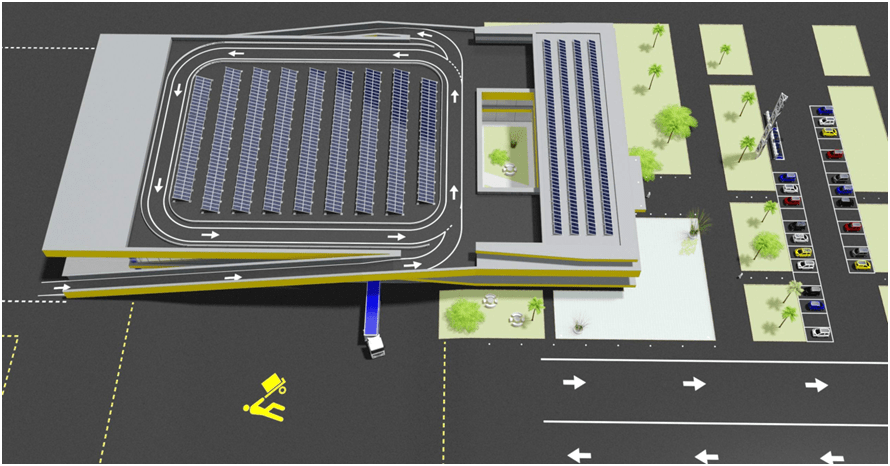
The microfactory will need tenth the extension and the investment of a standard factory for vehicles’ production. To reach this ambitious target several innovations are applied that cover from the possibility to make the configuration and the order of the vehicle from an application in your smartphone to the implementation of revolutionary laser cutting and 3D printing solutions. The microfactory has been sized for the production of 50 vehicles a day in two shifts, and is fed by renewable energy in order to be energy independent.
Avangard is linked to Steel S4 EV project, where the design of the vehicles has been optimised to be easily manufactured and at the same time to be best in class at occupant protection. Three of the first prototypes will be tested by Cidaut in the ambit of Steel S4 EV project to validate the frontal and lateral crash behaviour of the vehicles.
by cidaut | May 12, 2020 | Sin categoría
Cidaut has successfully finished CERO Project, with the cooperation of three automotive companies from Castile and Leon region: Grupo Antolín Ingeniería, ZF TRW and Casple S.A. The project has been funded by the “Instituto para la Competitividad Empresarial”. The main objective achieved thanks to the development of the project has been the research and development of new urban mobility solutions based on the integration of connectivity, automation and electrification. Cidaut considers that the electrification of the mobility should start in the urban environment for several reasons: importance of the air quality in cities, better energy performance of electric vehicles in urban driving conditions and easiness for infrastructure access. In several phases of the project, Casple’s urban electric vehicle prototype has been used to demonstrate the results achieved.S.A.
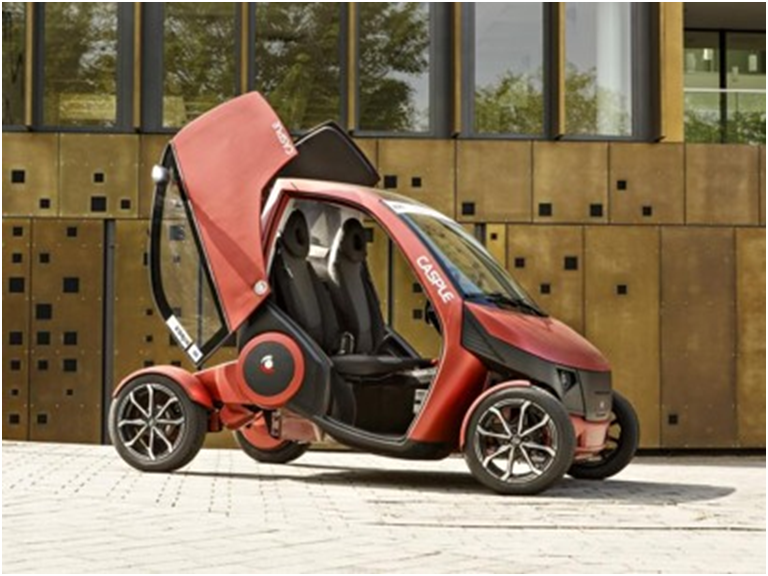
The project has been divided in three main tasks, the first one oriented to determine the needs of the future urban electric vehicles, the second aimed to obtain integral safety for this kind of vehicles and the third one looking for the enhancement of the communication capability of vehicles and infrastructure. The first task has allowed to establish a deep knowledge about the new urban transport needs from last mile logistics to mobility as a service solution that will have to overcome the tight mobility restrictions that will be progressively applied in different cities in the coming years and that have been also analyzed along CERO Project.
The second activity has covered all the aspects relative to safety from an integral point of view. The automated driving blurs the limit between active and passive safety, integrating both with the final objective of reducing the fatalities to CERO. The project has advanced in this direction presenting innovative solutions not only for the occupants but also for other vulnerable users of the road. In collaboration with ZF TRW, new restrain systems for automated driving levels 3 and 4 have been developed taking into account the new positions of the occupants in the automated vehicles. The pedestrians and cyclists safety has been improved through the development of artificial vision solutions, which identifies this kind of users, evaluates the risk of accident and alerts the vulnerable user and the driver/car (depending on the degree of automation) about the possible accident.
Finally low cost communication solutions have been developed for V2X applications. The solution adopted has allowed the implementation of different advanced solutions that will allow to increase the safety, improve the traffic flow and reduce the environmental impact of the traffic. Some of the communication applications tested along CERO project are: traffic jam detection, information about road works, allocation of points of interest, and speed recommendation to optimize green light flux.
by cidaut | May 12, 2020 | Sin categoría
The European Project STEEL S4 EV, funded by the Research Fund for Coal and Steel (RFCS) has successfully completed the first half of research and development activities. This item has coincided in the time with the presentation of the design of the second vehicle of the project: the threewheeler. The design presents several parallelism with the four wheels vehicle defined in the first stages of the project. The objectives behind this similarity are multiple, on one hand to simplify and make cheaper the manufacturing process, making possible to assembly both vehicles in the same assembly line, on the other hand to warranty the same level of integral safety as in the four wheels vehicle.
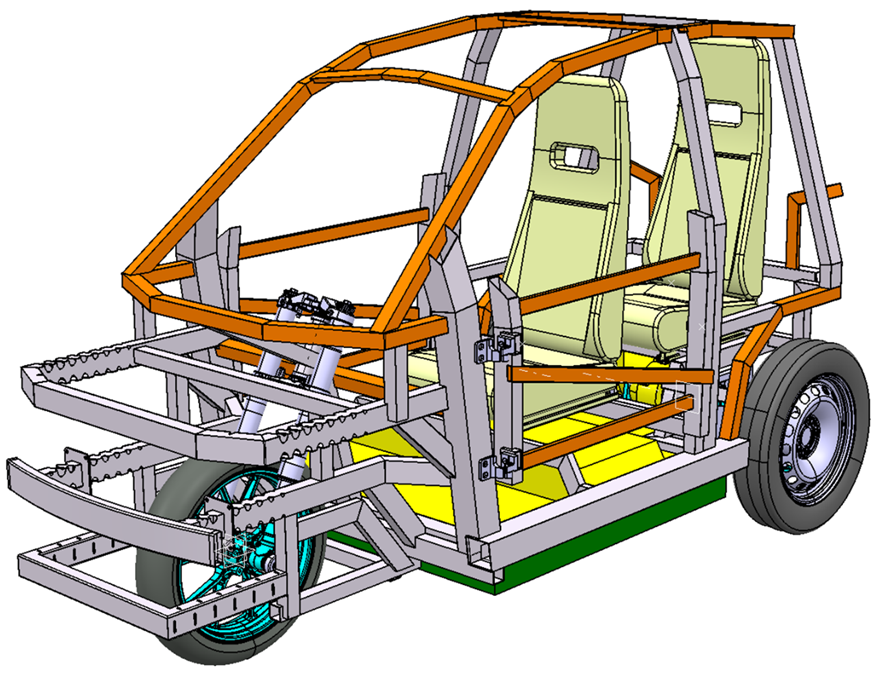
The solution adopted for the threewheeler is a two in line seats vehicle, with one wheel in the front, the electric motor in the rear axle, under the rear seat, and the battery pack under the front seat. The structure of the vehicle is made of different grades of Advanced High Strength Steel, where the geometry of the tubes and their thickness have been optimized to maximize the energy absorption in the frontal part of the vehicle and to warranty the undeformability of the safety cell, where the occupants are allocated.
In order to get this target, in parallel to the optimization of the crashworthiness through the finite elements methodology, advanced research is been done about the optimization of the welded joints of the advanced high strength steels. In every welding joint, not only the weld seam, but also the heat affected zone, suffers an important loss of mechanical properties due to the melting and uncontrolled cooling of the material. In the case of the Advanced High Strength Steels, this loss of properties is still more critical due to the special characteristics of the material. One of the objectives of STEEL S4 EV Project is to optimize the welding parameters, to improve the heat treatment of the joints in order to improve the static, dynamic and fatigue behavior of the welding joints of the complete structure of both vehicles, the three wheeler and also the four wheels vehicle.
In April, it has been held the Midterm Review Meeting of STEEL S4 EV Project, between the Project Coordinator, the Project Officer and some technical experts from the TGA 4. After a successful meeting, the activities of the project go on with the focus on the prototype manufacturing and the preparation of the different tests.
by cidaut | Oct 22, 2019 | Sin categoría
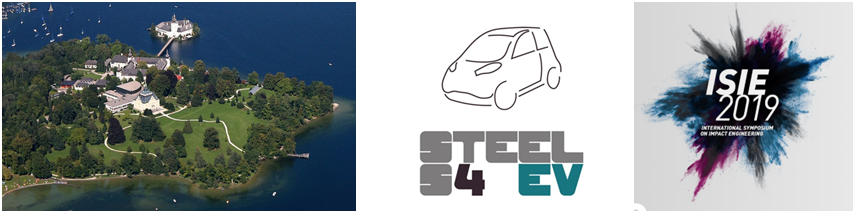
The international Symposium on Impact Engineering, ISIE 2019, aims to establish a professional dialogue between cultures, scientists and industry engineers on the field of experimental and computational mechanism with focus on impact and other dynamic problems.
The 2019 edition was hold in Gmunden in Upper Austria on 2-5th July 2019, the location offers a relaxed atmosphere, a beautiful environment, and a high-class service for the conference. Cidaut was there as Coordinator of Steel S4 EV project, presenting the preliminary results obtained in this project funded by the European Commission in the frame of the H2020 initiative. The presentation was focused on the crash results taking advantage of the participants’ expertize in impact engineering, mainly coming from Asia and Europe, but also with representative from America. The advances on the vehicle structure design and the evolution of the crash behavior from the starting of the project to the nowadays situation was presented.
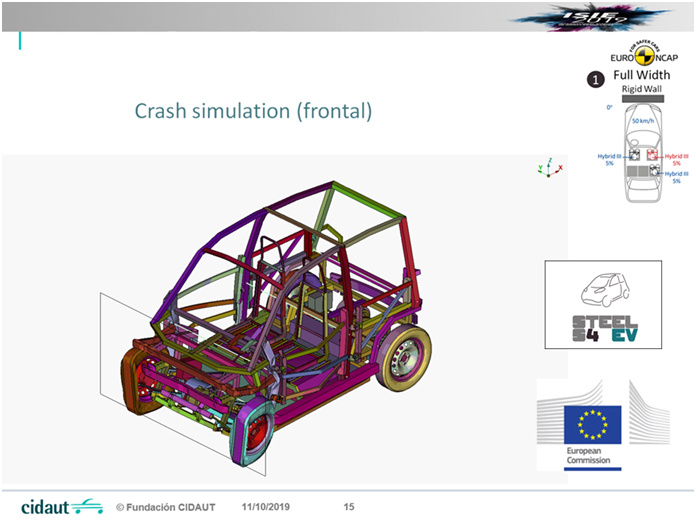
The project has covered the first year out of three, its main target is putting high strength steels at the forefront of a new trend in electric vehicles: light vehicles with three or four wheels that comply with crash regulation and with more restrictive Euro NCAP demands. Weld joint design and welding methodologies research to maintain the material properties in the weld area, assuring the robustness and long term durability.
Cost effective low-investment manufacturing will be achieved by a modular and flexible structural design: a complex 3D skeleton frame of welded tubes, bent with high accuracy using programmed laser cuts will enable the production of different vehicles sharing the same tooling.